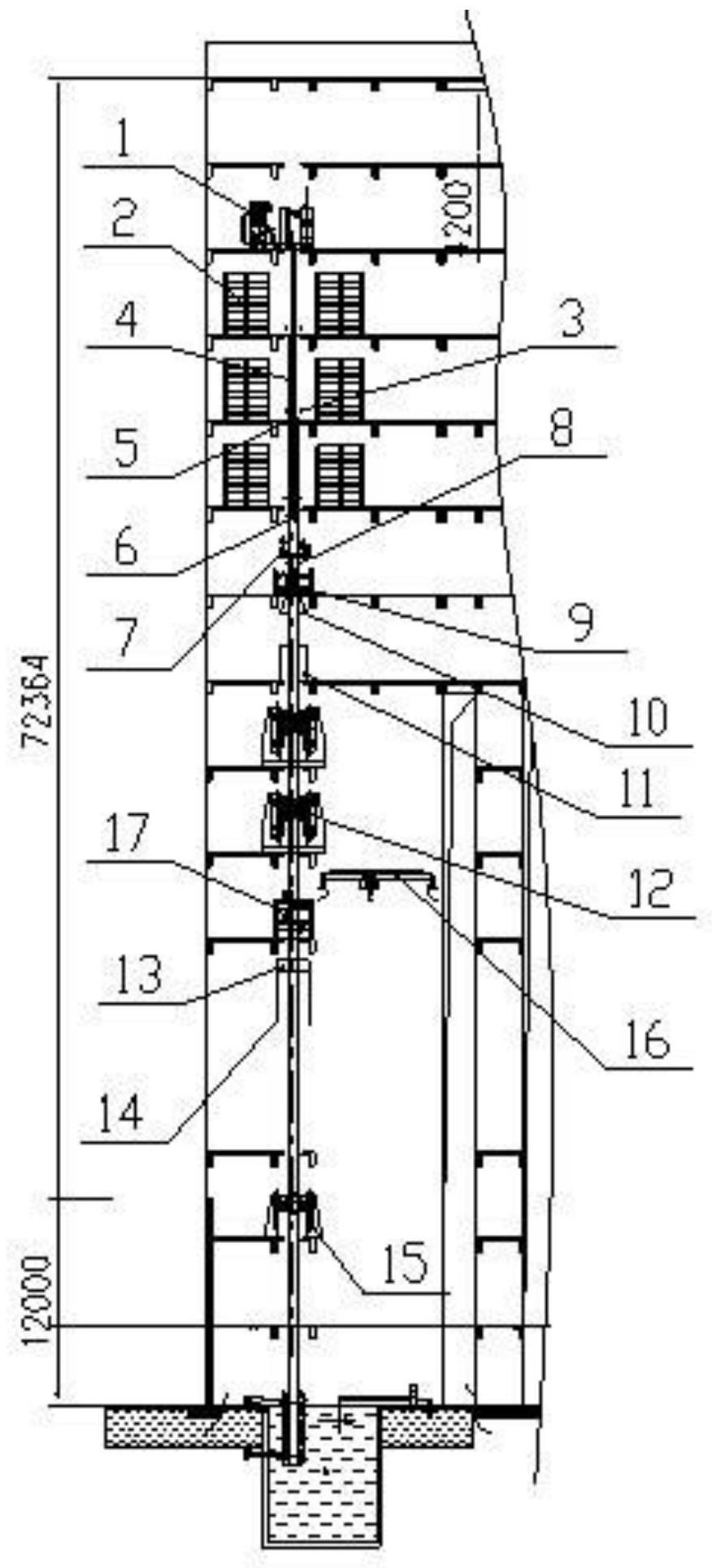
技术摘要:
本发明提供了一种基于竖直重垂张拉法的绝缘杆塔生产线,从上到下依次包括聚纱压纱区、内外模成型区、加热排气区、牵引区、表面处理区、注塑冷却区、断料沉浮结构和成品堆放区;所述的聚纱压纱区包括位于底部的集束区以及环绕集束区分布的若干过带张拉布架、带张拉纱架 全部
背景技术:
在电力行业,FRP复合材料也在发挥其重要作用,其中使用范围最广、成效最大的 莫过于输电线路杆塔。玻璃纤维复合材料杆塔相比如传统材料杆塔轻质高强、高绝缘、耐腐 蚀的技术优势特性已被世界各国所认同,因而成为全球电网建设中被积极研发与推广应用 的目标产品。国外复合材料电杆的制造与应用主要集中在北美和欧洲地区,其中研究开发 和应用最为成熟的是美国,美国的Ebert Composites公司、Powertrusion Composites公 司、Shakespear公司、North Pacific 公司和CTC公司等制品厂家都开发了自己的复合材料 杆产品,并申请专利和得到了比较广泛的应用。发展中国家如埃及、巴西、智利和伊朗等也 在积极开展复合材料杆塔的制造与应用工作,我国亦于近期对复合材料杆塔技术进行了研 究,如北京703研究所,鞍山远达、秦川、北玻院等单位,另外国网公司也对复合材料杆塔的 制备及应用技术进行研究,并积极推进试点工程实验。复合材料杆塔相关的研究将成为全 球输电线路发展的方向。复合材料杆塔已成为传统杆塔的理想替代品。 传统的输电杆塔,如木杆、钢管杆和混凝土杆,普遍存在质量大、易腐烂、锈蚀或开 裂等缺陷,耐久性差,使用寿命较短并且施工运输和运行维护困难,容易出现各种安全隐 患。相应的复合材料机械性能、电气性能优良,而其耐老化、耐腐蚀性能相比于金属、水泥材 料优势明显,是替代传统材料制备输电杆塔的理想材料。相比于铁质杆塔,复合材料杆塔优 异的绝缘性和憎水性可大幅增加绝缘间隙,因而能有效提高输电线路防雷、防污、防冰灾、 防风偏能力,同时缩减线路走廊宽度。如110kV复合材料杆塔接地线顺线方向悬空引下时, 塔头相地雷电冲击放电电压比常规110kV铁塔提高了约76%、杆塔相地空气间隙可达到 1.7m,远大于常规铁塔的1.0m,且在中雷区线路雷击跳闸率由0.70次/100km年降低至0.28 次/100km年以下。另外,优良的绝缘特性使得110kV聚氨酯复合材料杆塔比传统铁塔线路绝 缘子串的爬电距离增加了47%,提高了防污水平,缩减绝缘子片数,减小绝缘子串长度,因而 在较大程度上防止降低风偏放电事故的发生概率。同时,同塔双回复合材料杆塔的输电线 路走廊比传统钢管塔可缩减33%,比角钢塔缩减约46%。,GFRP复合材料杆塔综合成本优势突 出,其质量轻、耐腐蚀等特点可降低线路建设的运输、安装及维护成本,延长其使用寿命。以 110kV直线塔为例,计算结果显示,即使在保守设计条件下,复合材料杆塔的总重量只有钢 管塔的58%左右。在考虑原材料、运输安装、土地使用、产品寿命等成本因素的基础上,复合 材料杆塔线路的年均综合成本相比钢管塔与角钢塔可降低15%以上,而在应用技术上的优 势可减少线路在运行检修方面的成本,进一步凸显了其经济效益。 FRP复合材料的研究开发和应用在欧美发达国家以及日本, 已成为十分活跃的领 域。在今后一个时期, FRP作为一种高性能材料以其轻质高强、耐腐蚀、耐久性能好、施工便 捷等性能特点, 必将成为各类道路、桥梁、民用建筑结构的养护、检测和维修的必要补充材 料, 并得到广泛应用, 给我国的建筑经济领域带来不可忽视的综合效益。如此同时,FRP复 3 CN 111605229 A 说 明 书 2/9 页 合材料的应用,除了可大量降低电网系统的钢材用量,还可以打造低碳环保型绿色输电线 路的建设。钢铁的冶炼过程能耗高、污染重,且需要消耗大量煤炭、水资源。统计资料显示, 2018年,我国粗钢产量超10亿吨,而1吨粗钢的生产需消耗0.6吨煤炭和5吨水,同时排放出 290克粉尘、1450克SO2气体和85克CO2气体(中国钢铁工业协会统计数据)。大量钢铁产品的 使用给我国环境保护造成了较大的压力,特别是我国已确立了低碳环保在高新技术产业中 的重要地位,普通钢产品的产业发展受到严重制约。尽管树脂等化工产品的生产过程也会 产生排放问题,但相比于钢铁则低很多,而且,统计数据显示,化工行业每排放1吨温室气 体,可以为其他行业减排2.1~2.6吨温室气体,净减排量为1.1~1.6吨(中国化学工业协会 统计数据)。因此,FRP复合材料的应用对于建设绿色环保型新材料意义重大及国家新材料 战略具备重要意义。 尽管FRP复合材料的优点十分突出,但也存在显著的缺点: 1)材料的工艺稳定性差,FRP复合材料主要成型工艺有手糊成型、层压成型、RTM法、挤 拉法、模压成型、缠绕成型,其中材料稳定性较好的是拉挤成型、RTM法和模压成型,材料性 能的离散度比较小,但后面两种方法的生产工序比较复杂,生产效率低,目前市场上主要复 合材料产品还是倾向于拉挤成型工艺; 2)材料性能的分散性大,由于FRP复合材料的性能和纤维的铺层结构紧密相关,而FRP 材料中纤维的铺层很慢保证各处均一性,所以材料在不同位置取样后材料的力学性能会有 偏差,有的工艺生产的FRP材料分散性还比较大,这导致设计人员在设计FRP复合材料的结 构,都尽量取材料的测试值的下限,其结构导致材料设计时会出现性能过度富裕,导致材料 过度使用,材料浪费比较严重,制品成本偏高等一列问题; 3)长期耐环境老化性能差,FRP复合材料为有机树脂复合材料,有机树脂的耐候性,尤 其是耐日光中的紫外老化,是其户外应用的致命弱点,为了提升FRP材料的耐候性,开展了 很多相应材料耐候性研究,比较常见的有表面耐候涂层法,表面耐候材料复合法; 4)材料的模量低,FRP复合材料的强度甚至比钢铁材料的强度都,其拉伸强度可高达 1200-2000GPa,但材料的模量普遍偏低,以GFRP复合材料,其模量30-60Gpa,AFRP复合材料 模量50-90GPa,CFRP复合材料的模量60-200GPa,碳纤维复合材料模量越高,材料成本越高, 且材料各项异性,岩纤维的方向强度模量高,垂直纤维方向的材料模量低;而普通钢铁的模 量最低就达120GPa,一般铸钢的模量可接近200GPa,而且材料各项同性。模量低,制品在相 同载荷下,出现形变过大,一定程度上限制FRP产品的应用; 5)横向强度和层间剪切强度差,这是FRP复合材料典型的特点,材料在纤维分布方向强 度极高,而在纤维分布较少的纤维垂直方向力学强度极差,图中为国内某GFRP复合材料厂 家生产的玻璃纤维复合材料板材,纵向的复合材料的弯曲强度和模量明显高于对应横向, 而在增加表面纤维毡后,材料的横向弯曲强度和模量也逐渐增加;相应复合材料层间剪切 强度数据,平局值18MPa,也比较偏低,其截面图呈现纤维剪切开的蜂窝面结构。 基于以上FRP复合材料的缺点,FRP复合材料在国内的应用受限制,没有真正意义 的发挥复合材料轻质高强材料技术优势,在大基建和大尺寸样品的加工上的劣势尤为明 显,这样的结果导致FRP复合材料在工程结构材料使用有限,尤其在大基建上应用量也远低 于钢材,接下来将从几个方面分析复合材料在结构工程材料商应用受限制的原因。 国内复合材料杆塔自二十一世纪初开始研究,经过近20年的研究,国内已经完成 4 CN 111605229 A 说 明 书 3/9 页 了110kV复合材料杆塔结构设计和力学性能,通过第三方测试,产品在全国近一半的省份试 点应用,满足所有应用需求,并有效解决原线路雷击或防风等难题,但复合材料杆塔一直未 实现大规模化应用,制约其推广应用原因主要有两个方面: 1)复合材料设计的杆塔多为单杆型,其输送电压等级局限于110KV 以下,110kV及以上 电压等级复合材料杆塔直接过大,只能依靠手工铺层或大型缠绕机制备,杆塔的生产成本 过高,且生产效率极低,并且复合材料电杆生产过厚,材料成本也偏高。 大尺寸复合材料杆塔的手糊施工和小角度缠绕工艺的制备环节如下:吊装模具, 模具上打蜡上油,然后经手糊或缠绕完成杆塔预制品,预制品再固化,冷却,切割,脱模,成 品摆放等几个生产环节。手糊工艺需要的人工至少8人,而且手工铺放纤维布,生产环节繁 琐,工人所处生产环境也比较恶劣;缠绕成型改进了工人手工铺放布,改成纤维小角度缠 绕,纵向缠绕最小交角度可接近30°,理论纵向纤维缠绕交越小对杆塔强度贡献越大。尽管 大尺寸解决了手糊工艺的慢,但缠绕工艺的固化和脱模环节依旧存在,而且这两环节为生 产效率的瓶颈,平均一组复合材料电杆固化平均用时2-3小时,冷却0.5小时,吊装和脱模约 0.5小时,所以GFRP的单杆杆塔缠绕生产效率极低,一根电杆约6-8小时;同时缠绕杆塔由于 纤维不能完全纵向铺放,纤维在纵向的铺放不能达到最大化,部分强度会被环向分散掉,在 这种情况下,为了保证复合材料杆塔纵向强度,就只能加大纤维铺层厚度,保证复合材料杆 塔的纵向强度,杆塔的厚度会增加,重量也增加,导致复合材料杆塔材料成本过高。以上生 产环节,无论是材料成本,还是人工及生产管理成本非常高,相应产品的生产产能也极低, 导致FRP复合材料杆塔成本为传统钢管塔3-4倍,制约了FRP复合材料电杆的推广及应用。 2)复合材料杆塔尽管比传统杆塔具有更大的承载力,但由于材料弹性模量偏低, 纤维增强树脂基复合材料的模量50-70GPa,约为钢铁材料的一半,杆塔上端在极限工况载 荷下产生较大偏移,如10kV复合材料电杆的弯矩强度是水泥电杆的2-3倍,但其破坏弯曲形 变可以达到3倍,较大形变限制复合材料杆塔的应用,不利于复合材料电杆的产业化。 3)利用缠绕工艺生产的复合材料杆塔,必须借助相应的模具,由于模具生产复合 材料杆塔过程需要不断旋转,模具的形状只可能是圆形和正多形,不能加工成其“田”字形 或其它中空的异性结构。 传统横置拉挤工艺因生产的管材直径大,模具自重大制品上下偏心严重,外加拉 挤过程会和空气接触,容易在拉挤复合材料制品层间形成气泡及孔洞,造成管材空鼓、偏心 等问题;此外因引力作用,拉挤过程中上层浸润的树脂会自动向下流动而造成上层纤维缺 树脂,下层纤维层富含树脂,上层缺少树脂的部分会出现无法固化,制品截面发白,严重影 响管材强度,产品的稳定性极低。 横置拉挤模具是依靠模具一端的支点将模具固定,并通过支点调准拉挤制品偏心 问题,而在大尺寸FRP制品拉挤中,所用的模具很大,以110kV复合材料杆塔为例,杆塔最大 直径可以达到1500mm,那模具的重量会非常大,为保证大尺寸FRP制品在短时间能快速固化 弯曲,固化加热装置加长,相应的拉挤模具也要加长,如此模具的自重将会非常惊人,仅仅 依靠模具一端通过悬臂梁方式是没法固定拉挤模具,如果缩短拉挤模具长度,产品热固化 时间不够,制品无法完全固化。 5 CN 111605229 A 说 明 书 4/9 页
技术实现要素:
本发明为了解决现有技术的问题,提供了一种基于竖直重垂张拉法的绝缘杆塔生 产线,制备出的管材分为三部分,外层,加强筋,及内层。加强筋部分毡和玄武岩纤维纱采用 张拉设计,使整体的强度加强。 本发明提供的基于竖直重垂张拉法的绝缘杆塔生产线包括竖直分布的通过楼层 面分隔的若干层加工区域,加工区域中心开有同轴的加工通道,牵引装置垂直牵引经过预 应力张拉的原材料依次通过各加工区域的加工通道完成加工,所述的加工区域从上到下依 次包括聚纱压纱区、内外模成型区、加热排气区、牵引区、表面处理区、注塑冷却区、断料沉 浮结构和成品堆放区;所述的聚纱压纱区包括位于底部的集束区以及环绕集束区分布的若 干过带张拉布架、带张拉纱架和带张拉毡架,所述的集束区内设置有垂直向下伸入内外模 成型区的内模以及环绕内模外缘等距分布的芯模,带张拉布架、带张拉纱架和带张拉毡架 上的布纱毡通过张紧轮进入集束区后分别缠入内模和芯模之间形成缠绕内模的内层、缠绕 每根芯模的加强筋层以及缠绕在所有芯模外部的外层。 进一步改进,所述的内外模成型区从上到下依次包括压纱圈、第一树脂沉浸池、树 脂布缠绕区、第二树脂沉浸池以及对开外模分离机构,所述的对开外模分离机构包括支撑 墙、导滑轨道、紧固油缸、哈夫外模和高温加热固化模块,其中,哈夫外模通过导滑轨道固定 在两个支撑墙之间,两侧支撑墙分别通过紧固油缸拉伸推紧哈夫外模,工件通过哈夫外模 中心进行加热;所述的哈夫外模包括三层加热区域,温度自上而下逐层升高,相邻区域之间 通过隔热层分隔。 进一步改进,所述的表面处理区包括表面打磨区和表面清洁区,表面处理区内设 置有集尘设备。 进一步改进,所述的注塑冷却区包括ASA注塑装置和注塑冷却排气装置。 进一步改进,所述的断料沉浮结构包括切割机构、深井、沉浮桶和行吊机构,所述 的切割机构和行吊机构设置在河流上方,河流内开设深井,深井内设置有水泵系统,沉浮桶 设置在深井内部;所述的沉浮桶设置有加水口和出水口,沉浮桶通过推拉油缸与河流旁的 河道连接。 进一步改进,所述的加工区域最顶部设置有废气处理设备,所述的废气处理设备 包括依次连接的焚烧炉、冷却塔、布袋除尘器和排风机,焚烧炉上开有废气吸入口。 进一步改进,所述的纱、毡、布均为玄武岩高分子纤维材料,所述的环氧树脂沉浸 池中沉浸液为AG80环氧树脂。 进一步改进,所述的牵引区为交替工作的上下两台牵引机构,牵引机构为链条牵 引设备或液压牵引设备。 进一步改进,所述的芯模和内模内置陶瓷加热板,与外模加热固化区加热层级相 同,内模和芯模内部设置有废气收集管道,废气收集管道与废气收集系统相连。 本发明还提供了一种基于竖直重垂张拉法的绝缘杆塔生产线的生产方法,包括以 下步骤: 1)第一层布纱架和布毡架中纱和毡经过预张拉涨紧轮张拉,进入集束装置中第一层纱 架集束网板,经过集束分布后进入第一层定型板,定型后成为成品型材的内圈部分,围绕在 内模周围; 6 CN 111605229 A 说 明 书 5/9 页 2)第二层纱架毡架中的纱和毡经过预张拉,穿过第二层纱架集束网板,经过集束分布 后进入第二层定型板,定型后穿入芯模之间的孔位,成为成品型材的内圈和外圈中间的加 强筋部分; 3)第三层纱架和毡架中的纱和毡经过涨紧轮张拉后进入第三层纱架集束网板,经过集 束限位后进入第三层定型板,定型后成为成品型材的外圈部分,围绕在芯模和加强筋周围; 4)经过三层的集束和定型后的纱和毡,仍继续依靠芯模和内模的定位,进入不锈钢沉 浸池,浸泡专用配方配比的环氧树脂溶液; 5)经过充分浸泡后的材料需要在外层缠绕三层玄武岩纤维布,加强材料的外层韧性和 强度,缠绕后再次经过一层沉浸池沉浸,直到外层纤维布也充分浸泡后,材料进入加热固化 区域; 6)加热固化区域分为三层加热,100°、120°、160°三层逐级加热固化,各层加热区域之 间有隔热层; 7)芯模和内模也内置陶瓷加热板,与外模加热固化区加热层级相同,在外模沉浸区和 加热区上方都装有废气收集罩,在内模和芯模中也有废气收集管道,废气收集之后输送到 顶层废气处理系统; 8)材料经过高温固化后已经形成稳定结构,不需要内模、芯模和外模固定,然后通过恒 温加热,稳定整体的结构,恒温加热后的管材已经成型,然后进入牵引机构中,牵引机构分 为上下两台,交替工作,持续的对管材进行向下的牵引; 9)通过牵引机构后进入打磨清扫机构,打磨轮在侧边油缸的推力作用下,对管材表面 进行打磨光滑处理; 10)管材进入沉浮机构,利用水的浮力使沉浮桶浮在水中,在切割完成后接住管材,然 后利用行车吊装,通过水道运输出去,至此,成品的管材加工并完成运输。 本发明有益效果在于: 1、拉挤模具是垂直放置,模具可以通过顶部的固定连接装置连接到屋顶顶部固定,充 分利用地球引力,模具自然垂直,只需调准模具位置并加以固定,这种方式不管多大尺寸的 模具,都可以有效固定,也不用担心拉挤模具因自重引起拉挤制品偏心难题,同时可以尽量 加长模具尺寸,保证大尺寸拉挤FRP样品充分受热固化,材料性能更佳。 2、纵置拉挤工艺彻底解决横置拉挤工艺中制品气体难题及时排出,制品中包含气 泡技术,制品密实度不够的世界技术难题。拉挤过程,树脂带入的空气、树脂中挥发的小分 子及纤维中的水汽,在进入模具加热后,会向上逃逸,而横置拉挤固化装置上端没有排气 孔,气体难以及时逃逸出去,被固化在复合材料体中,便产生了大大小小的气泡,这也是拉 挤工艺不能太快的原因,越快气体逃逸越难,制品中的气泡就会越多。而纵置拉挤中,受热 后气体会自动向上逃逸,从固化装置上端排出,而不会因为不能及时逃逸而被固化到制品 中,形成气泡缺陷,制品密实。 3、纵置拉挤工艺彻底解决胶液沉浸不足、沉浸不均匀的世界技术难题。横置拉挤 过程,纤维浸润胶液,而当纤维进入固化装置前,因为胶液在重力作用下,会自动向下流淌, 其结果就会出现上部分的纤维缺少胶液浸润,无法固化,而底部纤维胶液富余的难题。纵置 拉挤,增加沉浸高度,并进行多次加压沉浸,纤维上胶液分布均匀,完全浸透。 4、纵置拉挤工艺可以安装类蜂窝煤结构的模具,拉挤出各种中空异型复合材料。 7 CN 111605229 A 说 明 书 6/9 页 利用FRP复合材料和设计的技术特点,最大化减轻复合材料重量同时,增加结构件的模量, 实现真正意义上的轻质高强。横置拉挤因为空间和安装特点,没办法安装复杂的模具,而纵 置拉挤可以利用上下空间的优势,安置不同结构复杂的拉挤模具,实现大型构件制品中空, 通过设计保证复合材料构件的强度和模量,去掉不必要的重量,能进一步有效降低复合材 料构件成本。这种中空结构复合材料构件将会是桁架式铁塔、桥梁构件和很多基建混凝土 钢筋材料的理想替代品。 5、纵置工艺彻底解决横置工艺废气无法收集的世界技术难题。纵置工艺纵置垃拉 挤工艺通过垂直摆放设备,通过集气罩、模具中的排气孔,将所有废气集中汇总到顶部环保 处理设备中,实现零污染排放;节约热能,减少能源的消耗,绿色环保。 6、在纵置拉挤彻底解决横置工艺兼容性差,工艺无法创高新革新的世界技术难 题。纵置工艺生产线包含所有横置拉挤工艺,新设备兼容性优异,工艺生产线可塑性强。 7、纵置拉挤工艺彻底解决纤维集约放置的世界技术难题。大尺寸的复合材料所需 的纱、毡、布支架,数以万计,横置完全无法进行放置排布。纵置拉挤工艺充分利用三维立体 空间,分层堆放、集约,彻底解决横置无法放置排布的问题。 8、纵置拉挤工艺彻底解决横置拉挤工艺无法预应力张拉的世界技术难题。纵置工 艺充分利用三维立体空间,进行垂直转向预应力张拉,大大增强复合材料的纵向刚度。 9、纵置拉挤工艺彻底解决了复合材料耐候性差、使用寿命有限的世界难题。纵置 工艺利用中空技术,开创复合材料高温喷釉工艺先例,在拉挤的连续型材表面直接高温喷 釉(或注塑成型一层耐候的高分子塑料),提升整个构件制品的耐候性能,在保证了制品户 外用应用的稳定性同时不会降低制品的生产加工效率和产能,所生产出的制品防晒、耐腐 蚀、抗老化,使用寿命达50年。(由于对比文件也公开了竖直工艺,竖直工艺本身的优点可以 不再描述,重点描述后面几点改进的有益效果) 10、内模、芯模安装:内模、芯模纵向分层安装固定的设计,便于模具的大尺寸化,易于 大尺寸型材的流水线生产。 11、内模、芯模的中空设计:内置排气管道,气体统一集中处理,环保化处理废气, 实现零污染排放。 12、沉浮切割机构:通过控制沉浮器下沉的位置来控制切割机构的工作,从而控制 管材的长度。通过沉浮器中水位的控制,解决超重物体的控制问题,解决切割后管材的移动 吊装问题,节约生产成本。 附图说明 图1为本发明整体结构示意图。 图2为聚纱压纱区示意图。 图3为内外模成型区示意图。 图4为树脂布缠绕装置示意图。 图5为所用内模示意图。 图6为所用芯模示意图。 图7为本发明制备出的成品结构示意图。 图8为断料沉浮结构示意图。 8 CN 111605229 A 说 明 书 7/9 页 图9为对开外模分离机构主视图。 图10为对开外模分离机构俯视图。 图11为废气处理设备示意图。 图12为内模芯模安装结构俯视图。 图13为内模芯模安装结构主视图。 图14为张拉结构示意图。 图15为更换升降架机构示意图。 图16为链条式牵引机构示意图。 图17为液压牵引机构示意图。 图18为打磨装置示意图。 图19切割机构示意图。