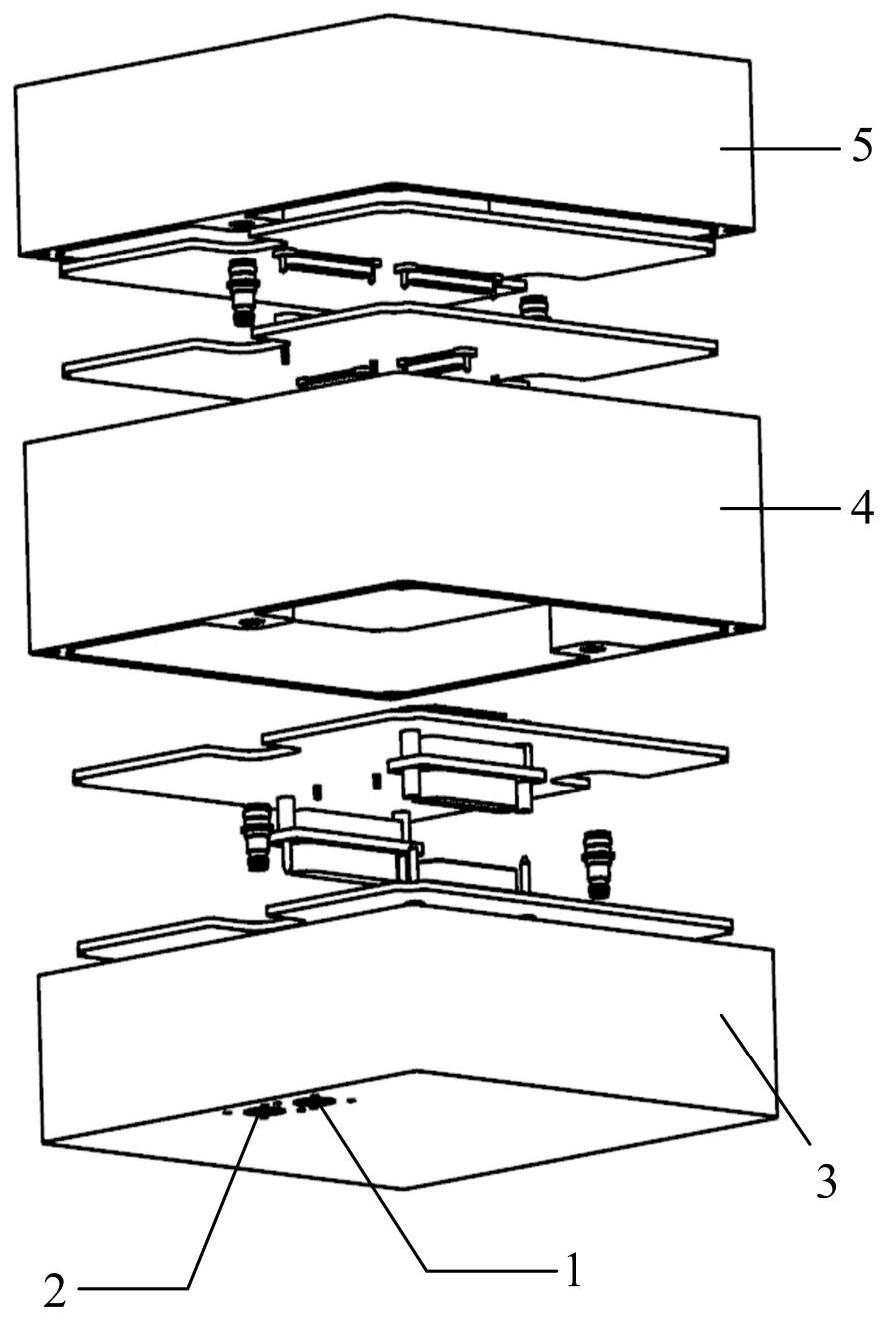
技术摘要:
本发明公开的一种多层串联式级联液冷板,旨在提供一种占用体积小,换热效率高的散热液冷板。本发明通过下述技术方案予以实现:利用设计有流道的两层材料焊接为一体成为冷板,每层液冷板的结构都制有固定贴合电路模块的内部空间,及其依次相互对插装配连接电路模块的机 全部
背景技术:
为了减小冷板流阻和提高换热效率,本发明的目的是针对现有技术存在的不足之 处,提供一种装配简单、占用体积小,换热效率高且可实现多层堆叠的多层串联式级联模块 散热液冷板,以解决多层电路模块堆叠设计的集中散热问题。 本发明解决所述问题的技术方案是:一种多层串联式级联液冷板,包括:采用自下 而上均为腔体结构的至少三层液冷板,每层液冷板相互独立,单独制作,其特征在于:利用 真空钎焊将设计有流道的两层材料焊接为一体成为冷板,对焊接成形的冷板进行二次加 工,形成电路模块安装零部件所需的机械接口,大功率电路模块放置于腔体内,贴合于内有 液冷流道的液冷基板之上,底层、中层以及中层、上层之间依次相互对插装配连接;以螺装 固定于液冷板的液冷连接头作为定位销盲插,依次相互对插装配连接底层、中层、上层;电 路模块间的互联采用可浮动连接器进行互联;循环冷却液通过底层液冷板进液口进入,利 用固定于中层、上层且上下垂直连通的并联分支流路冷却流道及液冷连接头循环至底层液 冷板的出液口流出,形成上下贯通的垂直互联的对流换热系统。 本发相比于现有技术具有如下有益效果: 装配简单、占用体积小。本发明采用每层液冷板之间,都以螺装固定于液冷板的液冷连 接头作为接驳定位销盲插,依次相互对插装配连接底层、中层、上层之间的接驳液冷连接 头,装配简单;中板间互联的液冷连接头采用径向密封设计,密封靠径向压力,密封头周围 不需要布置法兰和法兰安装螺钉。在对外循环冷却液进口仅有一对的条件下,仅依靠结构 的垂直互联就能完成所有模块散热问题,可解决多层电路模块堆叠设计的集中散热问题。 换热效率高。本发明采用每层液冷板都制有分别固定贴合电路模块的中空腔体, 及其依次相互对插装配连接电路模块的内壁,给集成电路模块更多的设计空间和散热面, 采用串联流路冷却流道和多级垂直互联液冷连接头,可以起到降低流阻和提高换热效率的 作用。另外,径向密封液冷投插入后对液冷板变形不敏感,结构件因温度、振动等因素产生 的轻微变形不会影响到液冷连接头的密封效果。 附图说明 图1是本发明多层串联式级联块液冷板的分解示意图。 图2是图1的主视图。 图3是图1中的液冷连接头结构图; 图4是图1液冷板一种实施例液冷流道的俯视图。 图中:1.冷却液进口,2.冷却液出口,3.底层液冷板,4.中层液冷板,5.上层液冷 板,6.底层电路模块,7.中层电路模块,8.液冷进口连接头,9.上层电路模块,10.液冷连接 头出口,11.外密封圈,12.内密封圈,13.液冷流道,14.低频连接器。
技术实现要素:
参阅图1、图2,在以下描述的实施例中,一种多层串联式级联液冷板,包括:采用自 5 CN 111601489 A 说 明 书 3/5 页 下而上均为腔体结构的至少三层液冷板,每层液冷板相互独立,单独制作。利用真空钎焊将 设计有流道的两层材料焊接为一体成为冷板,对焊接成形的冷板进行二次加工,形成电路 模块安装零部件所需的机械接口,大功率电路模块放置于腔体内,贴合于内有液冷流道的 液冷基板之上,底层、中层以及中层、上层之间依次相互对插装配连接;以螺装固定于液冷 板的液冷连接头作为定位销盲插,依次相互对插装配连接底层、中层、上层;电路模块间的 互联采用可浮动连接器进行互联;循环冷却液通过底层液冷板进液口进入,利用固定于中 层、上层且上下垂直连通的并联分支流路冷却流道及液冷连接头循环至底层液冷板的出液 口流出,形成上下贯通的垂直互联的对流换热系统。 优选地,三层液冷板材料可选用5A06、3A21、6061等牌号铝合金,工时须保证焊接 面平面度、粗糙度。 循环冷却液通过底层液冷板进液口进入,利用固定于中层、上层且上下垂直连通 的并联分支流路冷却流道及液冷连接头循环至底层液冷板的出液口流出,形成上下贯通的 垂直互联的对流换热系统。 多层串联液冷板的第一层结构包括:冷却液进口1、冷却液出口2、底层层液冷板3、 底层电路模块6。电路工作时,外部循环冷却液从冷却液进口1进入底层液冷板3,通过遍布 全板的底层液冷板冷却流道完成针对底层电路模块6的散热。 中层结构包括:中层液冷板4、中层电路模块7、液冷头进口8、液冷头出口10。中层 电路模块7包含两层电路板,两层电路板的互联可通过穿透中层液冷板4且不干涉液冷流道 13路径的低频连接器14实现。上层结构包括:上层液冷板5、液冷头进口8、上层电路模块9、 液冷头出口10。外部循环冷却液进口及出口位于底层液冷板底部方便外接使用;两对径向 密封液冷连接头分别螺装固定于中层、上层液冷板的底部。 上层液冷板的冷却流道遍布全板,冷却流道通过位于该板底部的一对径向密封液 冷连接头与中层液冷板的冷却流道互联,径向密封液冷连接头分别位于上层液冷板的相对 两侧。 中层液冷板和底层液冷板的冷却流道遍布各自的全板,底层液冷板的循环冷却液 进口及出口位置居于同一侧,径向密封液冷连接头均位于中层液冷板的同一侧,中层液冷 板的冷却流道通过位于该板底部的一对径向密封液冷连接头与底层液冷板的冷却流道互 联。 上层的径向密封液冷进口连接头位于与之相对的侧边位置,底层的冷却液进口及 出口、固定于中层的一对径向密封液冷连接头以及固定于上层的径向密封液冷连接头出口 均位于同一侧边位置。 底层、中层液冷板之间的液冷连接头接驳采用盲插安装方式,中层、上层液冷板之 间的接驳方式与上述相同,三块液冷板的液冷出口位置完全处于同一方向上,形成上下贯 通的垂直互联结构。 三层液冷板主要组合之间的互联包含了机械互联、电气互联和液冷互联,液冷连 接头须适应电气接口位置及精度;液冷连接头采用密封圈密封方式,旋入模块内部并固定, 在盲插时通过密封圈也可实现与被盲插模块的径向密封。 如液冷板内部采用微流道设计及加工工艺,液冷板由液冷流道所在分解面的上下 两部分进行焊接而成,液冷流道可以根据流量及压强进行设计,最小流道可做到1mm宽度。 6 CN 111601489 A 说 明 书 4/5 页 冷却液通过固定于底层液冷板的液冷头进口9进入了中层液冷板4冷却流道,完成 对中层电路模块7的散热,随后,通过固定于上层液冷板的液冷头进口8进入了上层液冷板 5,完成对上层电路模块9的散热后,经过上而下垂直互联的液冷头出口10以及对外循环冷 却液出口2,至此完成一次液冷循环。 参阅图3。液冷头直径偏小的为内密封圈13,管螺纹以及直径偏大的外密封圈12位 于液冷头的上端部分,装配时依靠管螺纹螺装于液冷板,而内密封圈13则对插入另外一块 液冷板;液冷头进口8与液冷头出口10结构均完全一致;三层液冷板的装配采用自下而上的 顺序,以一对液冷投为定位销装配,完成两次装配。 参阅图4。液冷板板体内部液冷流道采用微流道设计及加工工艺,液冷板由液冷流 道所在分界面的上下两部分进行焊接而成,焊接前将液冷流道在其中一侧上通过铣加工完 成,液冷流道宽度深度等可以根据流量及压强来进行具体设计,最小流道可做到1mm宽度。 以第二层液冷板4为例,展示液冷流道14路径。液冷流道14首先在下层上进行流道设计、加 工,然后与上层进行焊接,一般采用真空钎焊的方式。焊接完成后,再进行液冷头接口处加 工;加工时需保证密封圈所在位置的尺寸精度、粗糙度,并在适当的位置处进行倒圆角,以 便液冷头的安装。其中,遍布液冷板全板的液冷流道13路径采用常规的S形串联流道分支的 多级组合体结构。液冷流道13可以采用长且平直的平直流道延伸弯曲回路,两路单进、单回 的双/多并联S形串联流道分支进出的结构形式。单进S形串联流道分支包含一个入口和一 条出流路流动方向的S形串联流道,单出S形串联流道分支包含一个出口和一条回流路流动 方向的S形串联流道,组成一个伸弯曲回路流道并联了单进、单回的双并联S形串联流道。当 流体流过S形管道壁面环状凸环后,壁面的边界层发生分离,在越过环状凸环后形成漩涡, 之后再会合起来,继续前进,直到下一个节距环状凸环,流体在S形管道中不断地重复这一 过程。环状凸环的存在可使流体边界层不断发生这种周期性的脱离、会合和发展的扰动,在 近壁区产生旋转运动,不断扰动边界层,从而强化了传热过程。通过不断扰动边界层,阻止 其不断增厚,达到强化换热,提高换热效率的目的。平直流道平直圆形管路上增加每两级阶 梯孔之间的直径变化较小的多级阶梯孔,阶梯孔的收缩和扩张因其造成了管道内流体的扰 动和二次流,破坏了沿平直管道壁面逐渐增厚的边界层,多级阶梯孔所产生的局部压力损 失小,冷板流阻也只是略有增加,达到了强化换热的目的。这种结构在工程上简单易行,且 几乎不会增加制造成本。研究表明,带环状凸环的流道中流体的流动和换热过程均很复杂, 没有相关的理论公式进行计算,一般通过试验对其参数进行确定。试验时先将模拟热源按 实际工作状态安装在冷板的两侧,接触面涂上高性能导热硅脂,在冷板的入口和出口与液 冷源之间分别串接高精度压力测试仪,其读数的差值即为冷板的流阻。在冷板上取10个温 度检测点,用数据采集系统检测和记录冷板达到稳态后的各点温度数据。对比分析整理归 纳3种冷板试验得到的测试数据,并与有限元仿真的结果进行对比,试验结果与仿真结果的 趋势是一致的,采用并联分支和多级阶梯深孔起到了降低流阻和提高换热效率的作用,冷 板的流阻显著降低,而其换热效率则明显提高。低频连接器14安装在两并联S形管道分支流 道对称节距之间。 以上对本发明实施例进行了详细介绍,本文中应用了