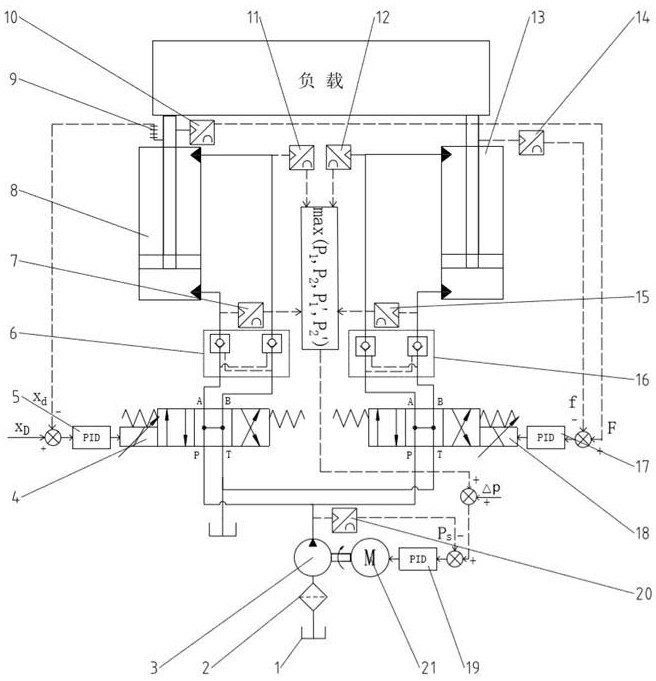
技术摘要:
本发明属于液压工程技术领域,具体涉及一种负载敏感双液压缸同步系统及其控制方法。主要包括两条同步驱动液压缸,同步控制器单元以及负载敏感单元。其中,从动缸的力指令取自布置于主动缸和负载之间的力传感器反馈信号,通过对从动缸输出力进行实时调节,保证其与主动 全部
背景技术:
随着现代机械加工工业及航空航天等技术的发展,越来越多的冶金设备、工程机 械及航空航天设备的驱动装置对高精度同步驱动技术的要求更加迫切,其中,液压同步驱 动系统由于结构组成简单、适宜大功率场合和易于控制等优点而占据了非常重要的位置。 目前液压同步驱动系统采用的同步驱动策略有“同等”方式和“主从”方式。“同等”方式是指 多个需同步工作的液压缸同时跟踪设定的理想输出,分别受到控制而达到同步驱动的目 的,此种方式实现同步驱动需要各个支路完全一样,即各支路的控制器、控制机构、执行机 构、检测和反馈机构等的性能有严格的匹配关系,这在实际应用中很难实现,因而控制效果 会随着硬件差异而降低。“主从”方式指多个需同步驱动的执行元件以其中一个的输出为理 想输出,其余执行元件来跟踪这一选定的理想输出并达到同步驱动,此种方式结构简单,更 容易实现,但从支路跟踪主支路时会存在延迟和动态误差,使得控制精度降低。 负载敏感系统是指一种能够自动感受系统中负载所需要的压力和流量信号,并将 此信号传递给负载敏感控制元件,使其系统压力参量发生变化,从而调整油泵的运行状态, 使得油泵输出液压功率几乎与负载所需要的液压功率相等,从而最大限度的减少能量损 失。目前,带有两个及以上执行机构的液压系统,其负载敏感单元的实现一般是通过梭阀来 对执行机构的最大负载压力信号进行比较,并自动地将较大的一个负载压力信号通过反馈 油路传递至负载敏感泵的负载敏感腔,进而控制变量泵的排量,使液压泵只提供执行机构 所需要的功率,以减小系统的能量损失,且回路中多使用流量补偿阀使控制阀前后压差不 变;但由于管道和流量补偿阀处的损失,导致负载反馈信号延迟量较大,除此之外,由于工 程机械中的变量泵的排量通常较大,其反应速度亦较慢,所以现有的负载敏感系统的响应 速度滞后较为严重。
技术实现要素:
为了解决上述问题,本发明提出了一种负载敏感双液压缸同步系统及其控制方 法。本发明的系统在结构上省去了流量补偿阀,且以电子信号反馈替代原有的液压回路反 馈。其中,两条同步驱动液压缸按照主从驱动方式工作,负载敏感单元在保证系统的功率供 给与“主从”两液压缸中较大的功率需求相匹配,提高驱动系统的能量利用效率的同时,当 “主从”两液压缸处于不同步工况,会使单向定量泵输出流量更多流向功率小(动作慢)的液 压缸,从而提高“主从”两液压缸的同步驱动性能。 本发明采取以下技术方案:一种负载敏感双液压缸同步系统,包括同步控制器单 元和负载敏感单元,同步控制器单元包括第一伺服阀、第二伺服阀、第一液控单向阀组、第 二液控单向阀组、主动液压缸、从动液压缸、位移传感器、第一力传感器、第二力传感器、第 4 CN 111577687 A 说 明 书 2/5 页 一控制器和第二控制器。负载敏感单元包括伺服电机、单向定量泵、第三控制器、第一压力 传感器、第二压力传感器、第三压力传感器、第四压力传感器和第五压力传感器。 其中第一伺服阀的A、B口通过第一液控单向阀组分别连接主动液压缸的无杆腔和 有杆腔,主动液压缸和负载之间布置有位移传感器和第一力传感器,位移传感器和第一力 传感器信号端接入电液总控制器的输入端。第一控制器输出端接放大器I,放大器I输出端 接第一伺服阀的电信号输入端,第二控制器输出端接放大器II,放大器II输出端接第二伺 服阀的电信号输入端,第二伺服阀的A、B口通过第二液控单向阀组分别连接从动液压缸的 无杆腔和有杆腔,从动液压缸与负载之间布置有第二力传感器,第二力传感器信号端接入 电液总控制器的输入端。 单向定量泵入口通过过滤器接油箱,出口接第一伺服阀和第二伺服阀的P口,第一 伺服阀、第二伺服阀的T口接油箱;第三控制器输出端接电机驱动器,电机驱动器输出端接 伺服电机电源输入端,第一压力传感器和第二压力传感器分别布置在主动液压缸的无杆腔 和有杆腔,第三压力传感器,第四压力传感器分别布置在从动液压缸的无杆腔和有杆腔,第 五压力传感器布置在单向定量泵出口处,第一压力传感器、第二压力传感器、第三压力传感 器、第四压力传感器和第五压力传感器信号端分别接入电液总控制器输入端。 进一步的,第一伺服阀和第二伺服阀的中位机能均为“H型”,当阀芯位于中位时使 液控单向阀打开管路压力为零,保证液控单向阀处于完全关闭状态。 进一步的,第一控制器为主动液压缸位置跟踪控制器,第二控制器为力同步控制 器,第三控制器为负载敏感控制器。 一种负载敏感双液压缸同步系统的控制方法。 1)对主动液压缸进行位置闭环控制,其位置指令依据工况需求人为设定,反馈环 节的位置信号取自布置于主动液压缸与负载之间的位移传感器,给定的位置指令和反馈的 位置信号进行比较并通过第一控制器处理,输出的控制信号经过放大器I放大控制第一伺 服阀阀芯位移,实现主动液压缸的位置闭环控制。 2)对从动液压缸进行力闭环控制,从动液压缸的力指令取自布置于主动液压缸和 负载之间的第一力传感器信号,反馈环节的力信号取自布置于从动液压缸与负载之间的第 二力传感器,力指令和反馈环节的力信号进行比较并通过第二控制器处理,输出的控制信 号经过放大器II放大控制第二伺服阀阀芯位移,即可对从动液压缸输出力进行实时调节。 3)负载敏感单元中,当主动液压缸和从动液压缸活塞杆伸出时,第一压力传感器 测得主动液压缸无杆腔压力 和第二压力传感器测得从动液压缸无杆腔压力 ,通过比 较将最大值反馈给第三控制器处理,输出的控制信号经过电机驱动器放大后控制伺服电机 的转速,来改变单向定量泵的转速,进而改变单向定量泵输出功率,使系统的功率供给与 “主从”两液压缸中较大的功率需求相匹配。 4)当主动液压缸、从动液压缸活塞杆缩回时,第三压力传感器测得主动液压缸有 杆腔压力 和第四压力传感器测得从动液压缸有杆腔压力,通过比较将最大值反馈给第 三控制器处理,输出的控制信号经过电机驱动器放大后控制伺服电机的转速,来改变单向 定量泵的转速,进而改变单向定量泵输出功率,使系统的功率供给与“主从”两液压缸中较 大的功率需求相匹配。 5 CN 111577687 A 说 明 书 3/5 页 5)在两液压缸伸出或缩回时,若“主从”两液压缸处于不同步工况,功率大的液压 缸上的伺服阀的阀口压差 减小,而功率小的液压缸上的伺服阀的阀口压差 增大, 根据公式 可知,此时单向定量泵(3)输出流量将更多的流向功率小的液压 缸,从而提高“主从”两液压缸的同步驱动性能。(其中 为流过伺服阀节流孔的流量, 为 流量系数, 为节流孔面积, 为液压油密度)。 6)当两液压缸处于停止工况,即单向定量泵出口压力为零,两液压缸工作腔压力 不为零,此时由电液总控制器输出待机信号控制伺服电机处于待机状态。与现有技术相比, 本发明具有以下有益效果: 1、本发明提出的负载敏感双液压缸同步系统及其控制方法中两条同步驱动液压缸按 照“主从”驱动方式工作:针对主动液压缸进行位置闭环控制,针对从动液压缸进行力闭环 控制,从动液压缸的力指令取自布置于主动液压缸和负载之间的力传感器反馈信号,通过 对从动液压缸输出力进行实时调节,保证其与主动液压缸具有同样的输出力,以实现主从 同步驱动。此方式结构简单,更易于实现。 2、本发明的负载敏感单元以电子信号反馈改变伺服电机转速替代原有使用液压 回路反馈改变变量泵排量来改变泵输出功率的控制方式,由第一,第二,第三,第四和第五 压力传感器检测两液压缸各腔压力和单向定量泵的出口压力,通过相应比较后反馈给第三 控制器处理,输出控制信号控制伺服电机转速来改变单向定量泵转速,从而改变单向定量 泵输出功率。提高了系统的反应速度和可靠性。 3、本发明省去了流量补偿阀,当“主从”两液压缸处于不同步工况,利用负载敏感 单元作用使单向定量泵输出流量更多流向功率小的液压缸,从而提高“主从”两液压缸的同 步驱动性能,且减少能量损失。 附图说明 图1是本发明的原理图; 图2是本发明的主从同步驱动单元控制框图; 图3是本发明的负载敏感单元控制框图; 图中:1-油箱,2-过滤器,3-单向定量泵,4-第一伺服阀,5-第一控制器,6-第一液控单 向阀组,7-第一压力传感器,8-主动液压缸,9-位移传感器,10-第一力传感器,11-第三压力 传感器,12-第四压力传感器,13-从动液压缸,14-第二力传感器,15-第二压力传感器,16- 第二液控单向阀组,17-第二控制器,18-第二伺服阀,19-第三控制器,20-第五压力传感器, 21-伺服电机。