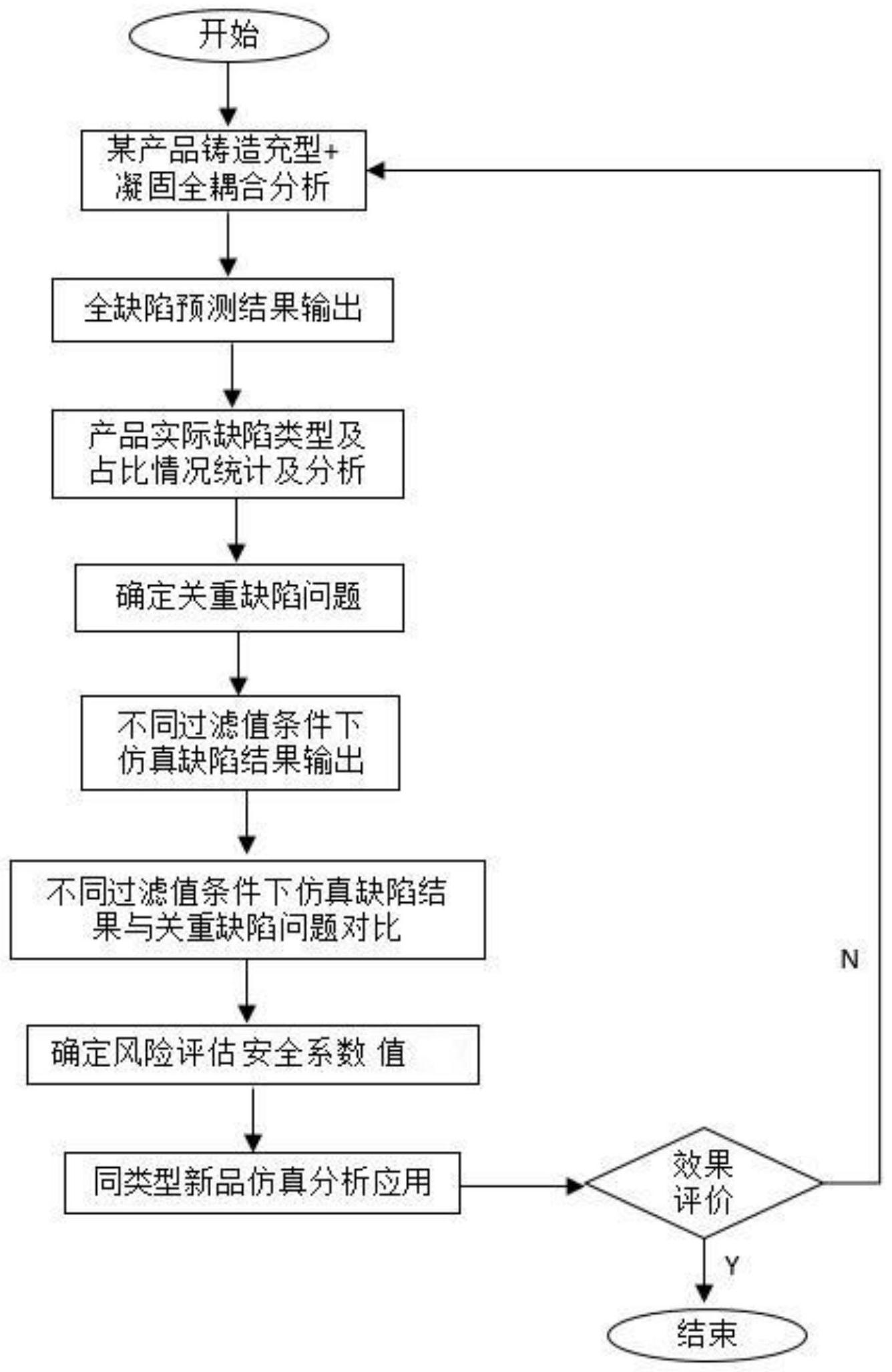
技术摘要:
本发明涉及一种基于铸件仿真软件的缺陷风险评估方法,包括以下步骤:步骤一,利用仿真软件对某产品进行充型和凝固全耦合仿真分析,并输出全缺陷结果;步骤二,统计和分析该产品在实际生产过程中的铸造缺陷种类及各铸造缺陷的占比,将铸造缺陷划分为需要整改的关重缺陷 全部
背景技术:
目前,铸造仿真技术已被越来越多的铸造企业所应用,它能够帮助工艺人员在开 发设计阶段提前预测可能产生的缺陷,从而提前采取措施控制缺陷的产生,以达到企业降 本、增效的目的。 国际一流的汽车企业如丰田、福特等都对铸造仿真技术做了大量的研究,其仿真 精度已达到85%以上,大大的提高了铸造仿真技术的可靠性。但由于仿真软件分析条件与 实际生产条件的差异,仿真缺陷结果与实际生产缺陷结果不可能完全吻合;同时结合铸造 仿真经验,仿真分析的缺陷结果往往比实际产生的缺陷多,造成“过”缺陷判断,导致花费大 量的时间去解决一些后期不会产生的缺陷或非关重缺陷,影响项目推进效率。因此,企业必 须结合自身条件,优化仿真输入和结果判据,以提高仿真分析精度。
技术实现要素:
本发明的目的是提出一种基于铸件仿真软件的缺陷风险评估方法,以提高仿真分 析精准性。 本发明所述的一种基于铸件仿真软件的缺陷风险评估方法,包括以下步骤: 步骤一,利用仿真软件对某产品进行充型和凝固全耦合仿真分析,并输出全缺陷 结果; 步骤二,统计和分析该产品在实际生产过程中的铸造缺陷种类及各铸造缺陷的占 比,将铸造缺陷划分为需要整改的关重缺陷与允许存在的非关重缺陷; 步骤三,依据步骤二中铸造缺陷的判据,对步骤一中的全缺陷结果输入不同过滤 值,并输出不同过滤值下的缺陷结果; 步骤四,将特征三中不同过滤值下的缺陷结果与步骤二中的需要整改的关重缺陷 进行对比,选出与步骤二中需要整改的关重缺陷最吻合的缺陷结果所对应的过滤值,该过 滤值为缺陷风险评估的安全系数值; 步骤五,将步骤四中所确定的安全系数值应用于同类型产品开发,并通过生产验 证安全系数值的有效性,若安全系数值与生产情况一致,则固化和运用该安全系数值;若安 全系数值与生产情况仍存在差异,则调整步骤三中的过滤值进行修正,直至与生产情况吻 合。 进一步,所述步骤三中不同的过滤值根据铸造缺陷的判据特征按一定间隔进行选 取。 进一步,所述步骤二中根据铸造缺陷的占比大小来划分需要整改的关重缺陷与允 许存在的非关重缺陷。 3 CN 111581743 A 说 明 书 2/3 页 进一步,所述步骤二中的铸造缺陷的判据为缩孔或热节或临界固相率。 本发明建立一种预测缺陷对产品良品率影响程度的安全系数值。利用这个安全系 数值将CAE分析多余或实际产生概率低(不对良品率产生影响)的缺陷过滤掉,解决了以往 CAE分析全身伤的问题,仅对关重问题进行解决,不仅提升了CAE分析的精准性,同时也保证 了项目的推进效率,节约工艺开发时间,充分保证设计与制造之间的最优性价比,降低了产 品开发成本。 附图说明 图1为本发明所述的基于铸件仿真软件的缺陷风险评估方法实施流程图; 图2为实施例中缸盖缩孔仿真判据结果图; 图3为实施例中缸盖3个月铸造缺陷种类及占比数据图; 图4为实施例中缸盖10%、20%、30%Porosity过滤值下的铸造缺陷结果图。