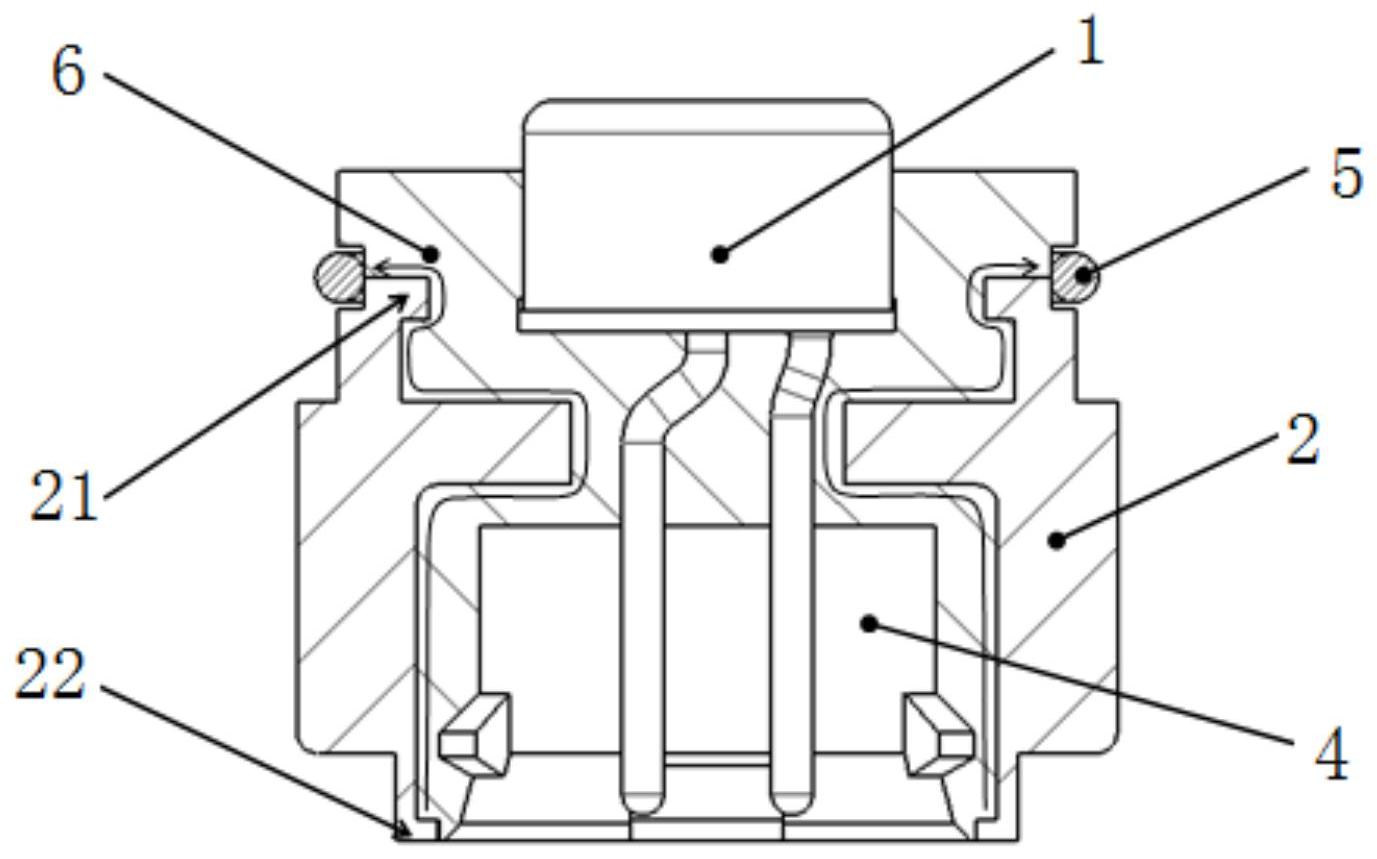
技术摘要:
本发明涉及汽车安全气囊气体发生器技术领域,具体地说是一种管状气体发生器用注塑体点火具组件,包括金属基座、注塑体、点火管、O形密封橡胶圈,点火管采用注塑体注塑在金属基座上,金属基座的内侧上部和下部分别设有突起结构和连接结构,突起结构、连接结构与注塑体镶 全部
背景技术:
汽车安全气囊模块由气体发生器和可以膨胀的充气布袋组成。当汽车发生碰撞并 发出点火信号时,气体发生器就会瞬时被点爆并产生大量的气体。这些由于产气药燃烧而 产生的大量气体,通过气体发生器外壳上按圆周分布的排气孔被排放到气袋内并使气袋膨 胀,从而达到保护乘员免受伤害的目的。由于气体发生器是汽车安全气囊的核心零部件,所 以随着汽车安全气囊普及程度的不断提高,对气体发生器性能、信赖性和价格的要求也越 来越高。 为了启动气体发生器工作,点火具是气体发生器中不可缺少的关键零部件。参见 图1和图2,点火具组件通常由一个点火管1和一个用于固定点火管1的金属基座2组成。点火 具组件组装加工的过程一般是先通过焊接的方法,将金属基座2固定在气体发生器的下壳 体3上;然后通过收口加工的方式,将点火管1连同O形密封橡胶圈5固定在金属基座2上。 为了降低气体发生器的零部件成本以及加工成本,通常采用以下两个途径:1,采 用注塑的方法直接成形联结线束的线束连接器接口4,以避免采用金属切削的方法加工复 杂形状的线束连接器接口4。2,直接将点火管注塑在具有简单形状的金属基座或气体发生 器的壳体上。 市面上现有的管状混合式和管状烟火式气体发生器,采用了注塑体的点火具组 件。由于注塑体颈部的截面积很小,有可能造成点火具组件在沿轴向方向上出现抗拉强度 不足的问题。 特开2003-161599的日本专利文献中公开了一种注塑体点火具组件。该点火具组 件中安装线束的线束连接器接口仍然需要用金属切削工艺进行加工,所以对于降低气体发 生器零部件成本的效果并不显著。 综上所述,为了降低管状混合式和管状烟火式气体发生器的零部件成本,应尽可 能地简化金属基座的形状,使连接线束的线束连接器接口采用注塑成形的方法进行加工。 但由于点火管穿过金属基座上的圆孔的截面积很小,使得充满圆孔部分的注塑体的小圆柱 部分的截面积也很小。由于施加在线束上的拉力将被直接传递到这个注塑体的小圆柱体 上,这就有可能造成整个注塑体点火具组件出现沿轴线方向上的抗拉强度不足的问题。 因此,需要设计一种管状气体发生器用注塑体点火具组件,在降低成本的同时,能 够保证在轴向方向上具有足够的抗拉强度。
技术实现要素:
本发明的目的是克服现有技术的不足,提供了一种管状气体发生器用注塑体点火 具组件,在降低成本的同时,能够保证在轴向方向上具有足够的抗拉强度。 3 CN 111547005 A 说 明 书 2/3 页 为了达到上述目的,本发明是一种管状气体发生器用注塑体点火具组件,包括金 属基座、注塑体、点火管、O形密封橡胶圈,点火管采用注塑体注塑在金属基座上,金属基座 的内侧上部和下部分别设有突起结构和连接结构,突起结构、连接结构与注塑体镶嵌,金属 基座与注塑体的上部交界处设有凹槽,O形密封橡胶圈镶嵌在凹槽内,注塑体的底部设有注 塑成型的线束连接器接口。 所述的连接结构为设置在金属基座的内侧下部的另一突起结构,另一突起结构镶 嵌在注塑体的底部凹槽内。 所述的连接结构为设置在金属基座的内侧下部的另一凹槽,注塑体表面的凸块镶 嵌在另一凹槽内。 所述的金属基座采用翻边结构固定在管状混合式气体发生器装药室的端部。 所述的金属基座采用收口结构固定在管状烟火式气体发生器装药室的端部。 金属基座插入管状气体发生器后,O形密封橡胶圈发生形变,形变后的O形密封橡 胶圈阻止水分从金属基座与装药室内壁之间的缝隙以及注塑体与金属基座之间的缝隙进 入装药室内腔。 本发明同现有技术相比,点火管被注塑在简单形状的金属基座上,金属基座设置 突起结构、连接结构与注塑体镶嵌,使点火具组件整体沿轴向方向上的抗拉强度得到保证; 注塑成型的线束连接器接口能有效降低点火具组件的成本,从而达到降低气体发生器成本 的目的;设置在金属基座与注塑体的上部交界处的O形密封橡胶圈能够阻止水分进入装药 室内腔,具有稳定和可靠的密封性能。本发明具有零部件成本低、结构简单以及便于加工和 组装的特点,适用于管状混合式气体发生器和管状烟火式气体发生器。 附图说明 图1 为现有技术中,点火具的装配示意图一。 图2为现有技术中,点火具的装配示意图二。 图3为本发明中,管状混合式气体发生器的点火具组件结构图。 图4为本发明中,管状烟火式气体发生器的点火具组件结构图。 图5为本发明实施例1中,点火具组件安装在管状混合式气体发生器上的示意图。 图6为图5的局部放大图。 图7为本发明实施例2中,点火具组件安装在管状烟火式气体发生器上的示意图。 图8为图7的局部放大图。