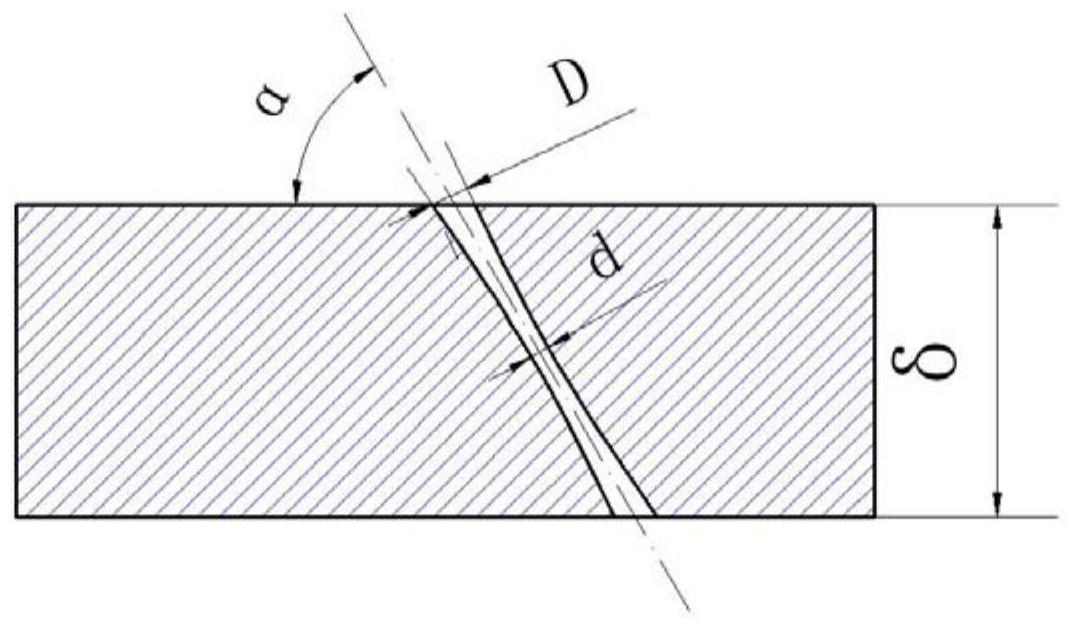
技术摘要:
本发明属于发动机冷却领域,具体涉及一种用于涡轴发动机的气膜冷却孔结构。所述气膜冷却孔以圆柱形气膜孔的中心线为旋转中心线,以抛物线为母线旋转360°得到孔的内表面,呈渐缩渐扩状;即所述呈渐缩渐扩状的气膜冷却孔包括截面积逐渐减少的进气段和截面积逐渐增大的出 全部
背景技术:
离散孔气膜冷却技术是一种高效的冷却技术,广泛应用于涡轴发动机火焰筒壁和 一些高温部件的冷却。其基本原理是从压气机引入冷却空气,冷却气通过气膜孔流出并覆 盖于高温部件的表面,从而达到隔绝热主流与高温部件表面接触的目的,降低表面温度,保 证设备可以长时间运行。 离散孔气膜冷却最基本的孔型是圆柱孔,圆柱孔具有加工简单、结构强度高的特 点,因此在航空领域的应用也最为普遍。但圆柱孔的气膜冷却效率明显偏低,也不能满足未 来发展的航空发动机冷却技术的要求,一方面是由于圆柱孔出口面积小,气膜覆盖宽度小, 冷气出口动量大,高吹风比时冷气易吹离壁面;另一方面是由于冷气喷出时与主流剪切作 用导致肾型涡的出现,使得冷气不容易贴附于壁面,使得下游冷却效果较差。 由于圆柱孔的气膜冷却效果不佳,近年来国内外陆续发展了一系列新的气膜冷却 孔型以提高圆柱孔的气膜冷却效果,比如扩张型孔、缝型孔、双喷射孔、姐妹孔、沟槽孔等。 上述孔型在气膜冷却效率方面都比圆柱孔有了大幅提高,其中扩张型孔已成功应用于实 际,不仅冷却效果远优于普通圆柱孔,同时比较容易加工实现;但是传统的扩张型孔还依然 无法主动产生有利于气膜冷却的流场涡系结构。
技术实现要素:
本发明的目的在于提供一种用于涡轴发动机的气膜冷却孔结构。 实现本发明目的的技术解决方案为:一种用于涡轴发动机的气膜冷却孔结构,所 述气膜冷却孔以圆柱形气膜孔的中心线为旋转中心线,以抛物线为母线旋转360°得到孔的 内表面,呈渐缩渐扩状;即所述呈渐缩渐扩状的气膜冷却孔包括截面积逐渐减少的进气段 和截面积逐渐增大的出气段。 进一步的,所述气膜冷却孔的出口直径D与喉部直径的d的比值在1.0~2.5之间, 气膜冷却孔的中心线与流体流动方向的夹角α在25°~40°之间。 进一步的,所述气膜冷却孔的喉部直径d为0.4~1mm。 进一步的,所述气膜冷却孔为多排,每排气膜冷却孔包括多个,多排气膜冷却孔之 间交叉排列。 进一步的,所述多个气膜冷却孔的展向间距P与喉部直径d的比值P/d在0.5~3之 间,流向间距S与喉部直径d的比值S/d在1~5之间。 进一步的,所述冷却壁面厚度δ在2~5mm之间。 本发明与现有技术相比,其显著优点在于: (1)本发明的气膜冷却孔结构能够有效的改进气膜孔的进出口处的流场情况,提 高孔内的对流换热能力; 3 CN 111578310 A 说 明 书 2/3 页 (2)本发明的气膜冷却孔的渐缩段能够提高孔内气流的流动速度,改善低吹风比 时的冷却效果; (3)本申请的气膜冷却孔孔的出口面积大,提高了气膜的覆盖宽度,有利于使得冷 却气体更加贴合壁面。 附图说明 图1a为本发明的气膜孔冷却结构基本形式的俯视图。 图1b为本发明的气膜孔冷却结构基本形式的剖面图。 图2a为本发明的气膜孔冷却结构展向间距、流向间距和三个截面布置示意图。 图2b为本发明的气膜孔冷却结构多个孔布置示意图。 图3a为本发明的气膜孔冷却结构中气膜孔上的前缘、侧缘以及后缘三条母线分布 示意图。 图3b为吹风比M=1.5,倾角α=30°时的传统的圆柱形气膜孔的三条母线上的局部 对流传热系数曲线图。 图3c为吹风比M=1.5,倾角α=30°时的本发明气膜孔的三条母线上的局部对流传 热系数曲线图。 图4为吹风比M=1.5,倾角α=30°时的传统的圆柱形气膜孔结构和本发明新型的 气膜孔结构的热侧壁面上的冷却效率的对比图。 图5a为传统的圆柱形气膜孔结构出口下游各截面上的气膜冷却效率等值线对比 图(D=4mm)。 图5b为本发明气膜孔结构出口下游各截面上的气膜冷却效率等值线对比图(D= 6mm); 图5c为本发明气膜孔结构出口下游各截面上的气膜冷却效率等值线对比图(D= 8mm); 图5d为本发明气膜孔结构出口下游各截面上的气膜冷却效率等值线对比图(D= 10mm)。