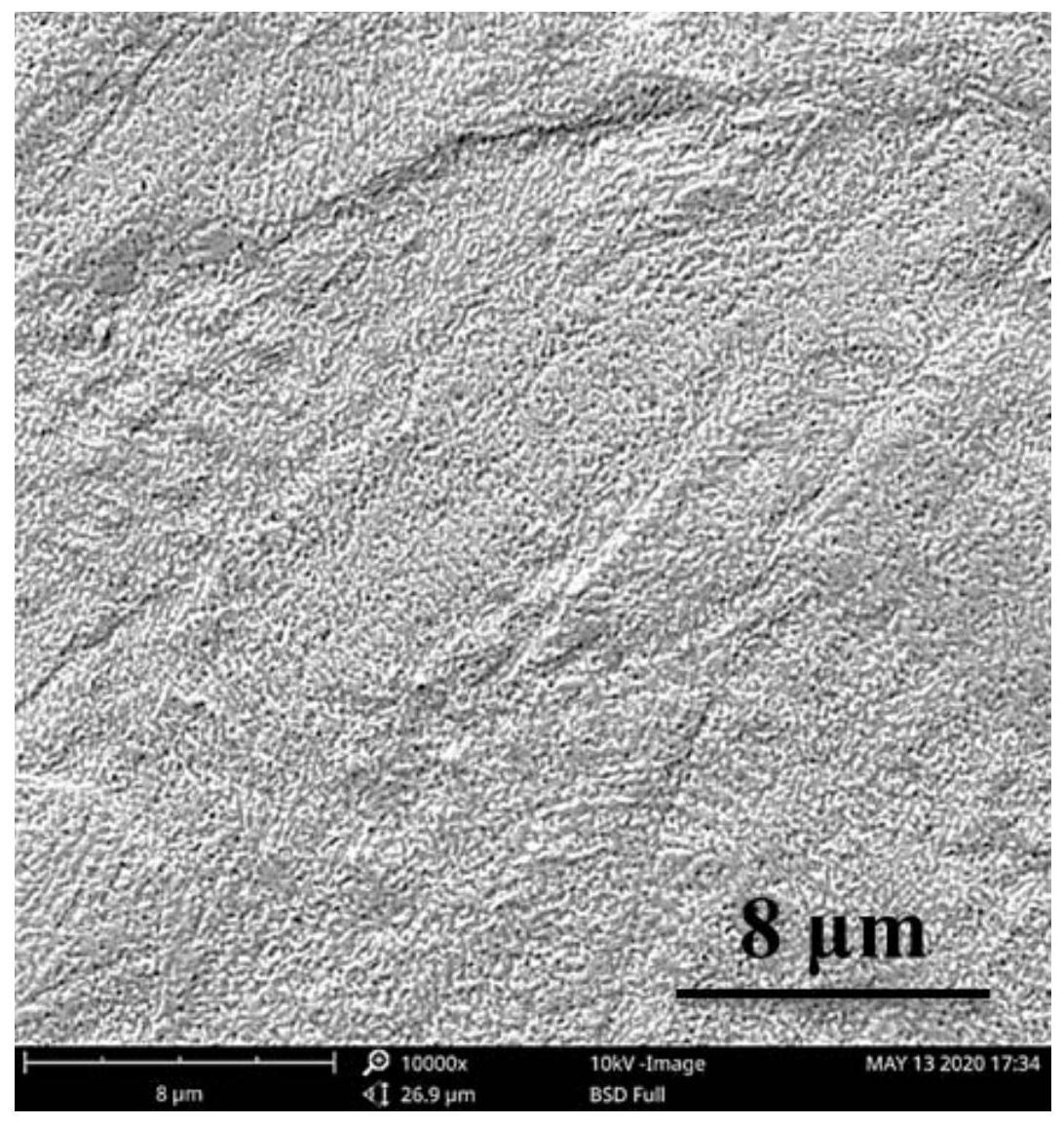
技术摘要:
本发明属于表面工程与表面处理技术领域,具体公开了一种铁族元素和钨的合金与碳化硅复合镀层及其制备方法与应用。所述方法为(1)配制复合镀液:Fe2 /Fe3 盐、Co2 /Co3 盐、Ni2 /Ni3 盐、钨酸盐、络合剂、分散剂、碳化硅;溶剂为水;所述复合镀液的pH为7~14;(2)将基体 全部
背景技术:
电镀铬工艺成本低、效率高,镀层光洁度好、耐磨耐蚀性强,广泛应用于航空航天、 车辆舰船等装备关重件表面强化以及磨损、腐蚀后的修复,但电镀铬工艺严重污染环境,影 响人体健康,已逐步被限制使用。目前,尚无成熟的绿色表面技术体系可替代电镀铬技术广 泛应用于装备的修复与强化。针对上述问题,研发可替代电镀铬的高性能镀层制备技术及 其适配材料体系,是装备保障领域亟需解决的重大问题之一。 代铬镀层是指外观、硬度、耐磨擦磨损性能、抗腐蚀能力等方面均接近于铬镀层的 合金镀层,主要包括铁族(铁、钴、镍)合金,及铁族元素与磷、硼、钼、碳及钨等组成的二元或 多元合金。目前,被广泛研究的代铬工艺主要有电镀Fe-W、Co-W、Co-Ni、Ni-W、Ni-B、Ni-P、 Ni-Mo、Fe-Ni-W、Co-Ni-C和Co-Ni-B等合金。以上合金都具有较高的硬度、抗腐蚀能力及耐 摩擦磨损性能,但仍不及铬镀层,仅在热处理后部分镀层的硬度才能达到铬镀层的水平。但 热处理需在惰性气体保护下进行,因此,上述代铬镀层的制备周期长、工艺复杂、且成本较 高,至今尚没有一种被广泛应用。复合电镀是通过电解法在基材上沉积结合力良好的金属 与固体颗粒(包括:金刚石、碳化物、氮化物、硼化物、氧化物等)的复合覆盖层方法,复合镀 层的性能由镀层金属与夹杂其中的第二相共同决定,因此,具有比纯金属镀层更为优异的 机械强度、抗摩擦磨损能力和耐蚀性能。此外,在镀层金属确定的前提下,第二相的组成、尺 寸及含量便成为决定复合镀层性能的关键因素,从而能够实现对复合镀层性能的调控。 M.K.Das等(Surface and Coatings Technology,2017,309:337-343.)采用复合镀技术制 备的Ni-W/金刚石复合镀层在未经任何后处理的情况下即达到了铬镀层的硬度水平,突破 了传统代铬合金镀层需要热处理的技术瓶颈。但是,该方法同样受限于金刚石高昂的成本, 而难于普及。 综上所述,铁族元素(铁、钴、镍)和钨的二元或多元合金与低成本增强相颗粒组成 的复合镀层有望成为高性能、实用性代铬镀层的最佳选择。碳化硅,作为增强相颗粒,虽然 其成本较低,但其微米尺度下制备复合镀层的机械强度不及金刚石基复合镀层,因此需要 选用纳米碳化硅,而由于纳米尺度的颗粒非常容易团聚,常规搅拌仅能抑制其沉降,而并不 能抑制其团聚。所以,如何抑制纳米碳化硅颗粒在镀液中的团聚,是其与基质镀层结合需要 克服的困难。
技术实现要素:
为了克服上述现有技术的缺点与不足,本发明的首要目的在于提供一种铁族元素 和钨的合金与碳化硅复合镀层的制备方法。 3 CN 111607817 A 说 明 书 2/6 页 本发明另一目的在于提供上述方法制备得到的铁族元素和钨的合金与碳化硅复 合镀层。 本发明再一目的在于提供上述铁族元素和钨的合金与碳化硅复合镀层在装备增 材修复与再制造中的应用。 本发明的目的通过下述方案实现: 一种铁族元素和钨的合金与碳化硅复合镀层的制备方法,包括以下步骤: (1)配制复合镀液:Fe2 /Fe3 盐10~100g/L、Co2 /Co3 盐0~100g/L、Ni2 /Ni3 盐0~ 100g/L、钨酸盐20~200g/L、络合剂30~300g/L、分散剂0.1~10g/L、碳化硅1~20g/L;溶剂 为水;所述复合镀液的pH为7~14; (2)将基体放入复合电镀液中进行电镀;电镀所用的电流为直流、单脉冲电流、双 脉冲电流或直流/脉冲叠加电流;并在电镀时进行机械、空气、喷流或超声搅拌。 步骤(1)中所述络合剂为酒石酸、焦磷酸、次磷酸、柠檬酸、氨三乙酸、草酸、乳酸、 烟酸、氨基磺酸、氟硼酸、羟基乙叉二磷酸、5,5′-二甲基乙内酰脲、氨水及它们的盐类中至 少一种。 步骤(1)中所述分散剂为十六烷基三甲基溴化铵、十二烷基硫酸钠、聚氧乙烯醚 类、聚丙烯酸钠和聚乙烯吡咯烷酮中的至少一种。 步骤(2)中所述基体为任何不溶于镀液的导体及经金属化的绝缘体,优选为银、 铜、铁、铝及经化学镀铜或镍的陶瓷、木材、玻璃、塑料等。 优选的,步骤(2)中根据待镀基体材质及表面油污状态的不同,可先对其进行前处 理,具体可采用氢氧化钠水溶液、洗洁精、去污粉、丙酮、酒精、汽油等有机溶剂对基体进行 除油5~10min,然后用水冲洗;再采用稀硝酸、稀盐酸对基体进行除锈,根据基体表面锈蚀 程度的不同,在室温条件下处理时间一般为10~60s,最后用水冲洗。 步骤(2)所述单脉冲电流具体参数为:导通时间Ton=0.1~1ms,关断时间Toff=0.4 ~1ms,频率f=500~2000Hz,电流密度Jm=0.5~10A/dm2;所述双脉冲电流具体参数为:Ton =0.1~1ms,Toff=0.4~1ms,脉冲通断周期T=0.5~2ms,f=500~2000Hz,正向电流密度 J =0.5~10A/dm2,反向电流密度J -=0.025~1A/dm2m m ;所述直流/脉冲叠加电流具体参数 为:f=500~2000Hz,J=0.5~10A/dm2,Jm=0.5~10A/dm2(直流/单脉冲叠加)或f=500~ 2000Hz,J=0.5~10A/dm2,Jm=0.5~10A/dm2,J -m =0.025~1A/dm2(直流/双脉冲叠加)。 步骤(2)所述机械搅拌的速度为600~3000r/min,空气搅拌的流量为10~200m3/ h,喷流搅拌的流量为10~200m3/h,超声搅拌的频率为1~100kHz。搅拌速率的大小可影响 碳化硅颗粒的分散性能,并消除浓差极化,进而影响复合镀层的形貌、组成和结构;强烈的 搅拌还能够提高阴极电流密度上限和电流效率。 步骤(2)所述电镀温度为5~95℃,电镀时间为0.1~10h。 一种铁族元素和钨的合金与碳化硅复合镀层,通过上述方法制备得到。 优选的,所述复合镀层中基质合金为Fe-W、Fe-Co-W、Fe-Ni-W或Fe-Co-Ni-W。 优选的,所述复合镀层中增强相为微米级(0.1~10μm)、纳米级(1~100nm)或微纳 米混合SiC颗粒。 优选的,所述复合镀层的厚度为1~3000μm,基质合金的晶粒尺寸为0.01~10μm, 碳化硅含量为5~50at.%,且分布均匀。 4 CN 111607817 A 说 明 书 3/6 页 所述复合镀层的阳极包括铁、钴、镍、钨及任何不溶于镀液的惰性阳极,例如:不锈 钢、铂、石墨、钽铱钛、钌钛铱等。 所述铁族元素和钨的合金与碳化硅复合镀层在装备增材修复与再制造中的应用。 本发明相对于现有技术,具有如下的优点及有益效果: 1 .本发明所采用的基质合金镀层为铁族金属元素与钨的二元或多元合金(Fe-W、 Fe-Co-W、Fe-Ni-W或Fe-Co-Ni-W),是现有代铬镀层中硬度最高的合金镀层之一。 2.本发明所采用的碳化硅颗粒,是现有复合镀层增强相中成本最低的陶瓷颗粒之 一。 3 .本发明在钢铁表面所制备的Fe,Co ,Ni-W-SiC复合镀层经90°弯曲试验并无脱 落;满足国家标准GB5270-200X金属基体上的覆盖层附着强度试验方法对电镀层的要求。 4.本发明制备的Fe,Co,Ni-W-SiC复合镀层耐蚀性能良好,满足国家标准GB5938- 86《轻工产品金属镀层和化学处理层的耐蚀试验方法》的5%食盐水中性盐雾试验指标。 5.本发明制备的Fe,Co,Ni-W-SiC复合镀层在未经热处理的情况下即可达到铬镀 层的硬度水平。 6.本发明中聚乙烯吡咯烷酮起到了抑制纳米碳化硅团聚和改善镀层晶粒尺寸的 双重作用(这是因为聚乙烯吡咯烷酮加入后,复合镀层中的铁钨合金的晶粒尺寸相比未加 之前降低了)。通过物理机械搅拌的方式有助于碳化硅的分散,但对抑制纳米碳化硅的团聚 几乎没效果。 附图说明 图1为实施例1中Fe-W-SiC微米复合镀层(微米SiC)的SEM照片。 图2为实施例1中Fe-W基质镀层的SEM照片。 图3为实施例1中Fe-W基质镀层的EDS谱。 图4为实施例2中Fe-W-SiC纳米复合镀层(纳米SiC)的SEM照片。 图5为实施例2中所述镀液在未添加分散剂情况下制备Fe-W-SiC纳米复合镀层的 SEM照片 图6为实施例7中Fe-W-SiC纳米复合镀层的纳米压痕曲线。